Skip to content
UA PLUMBERS LOCAL #15
Maple Grove MN
U.A. Plumber’s Union Local #15 was experiencing growth pains. Their union hall was located in an older building in the heart of the Minneapolis CBD. Their training facility was co-located with a growing technical college in need of additional space. Michael helped U.A. Plumber’s Union Local #15 to locate a site and partner with the right experts to accomplish their real estate goals.
U.A. Plumber’s Union Local #15 occupied two facilities that were not meeting their needs. The goal was to combine the union offices/hall as well as the existing training center under one new modern facility to assist with recruiting and training efforts.
CHALLENGES
The Union had financial benefits to moving as early as possible and desired to relocate outside of downtown Minneapolis in order to better serve their member needs for meeting attendance and member training. Existing industrial facilities were difficult to find in the midst of strong demand for industrial buildings, but the use and ceiling heights were needed for much of the required training. Parking needs were much greater than traditionally provided for an industrial building, so a site was needed to support their desired level of parking.
RESULTS
Michael embarked on a process that included interviewing and recommending architects and general contractors. After an extensive interview process, these providers were selected, and he negotiated their fees and contract agreements. Michael managed a detailed programming and budgeting process to ensure the Union’s needs were met initially and in the future. An IT/AV consultant was engaged to ensure state-of-the-art classrooms and technology.
Michael led the site selection process, presented alternatives, worked with the architect and contractor to evaluate each alternative, and recommended the best option. Ultimately, a 96,000-square-foot industrial building was selected, and a purchase price was negotiated for the building. The architectural and budgeting process was managed to ensure the project met the union’s $21.6 million dollar budget.
Michael worked with an interior designer to select and bid all furniture, fixtures, and equipment. They worked closely with a security company to select systems and secure the building and managed the bidding process, as well as the construction process, to ensure on-time and under-budget delivery. Michael managed the payment and lien waiver process to ensure proper and accurate payment. Lastly, he managed the move and close-out process to ensure punch list items were completed.
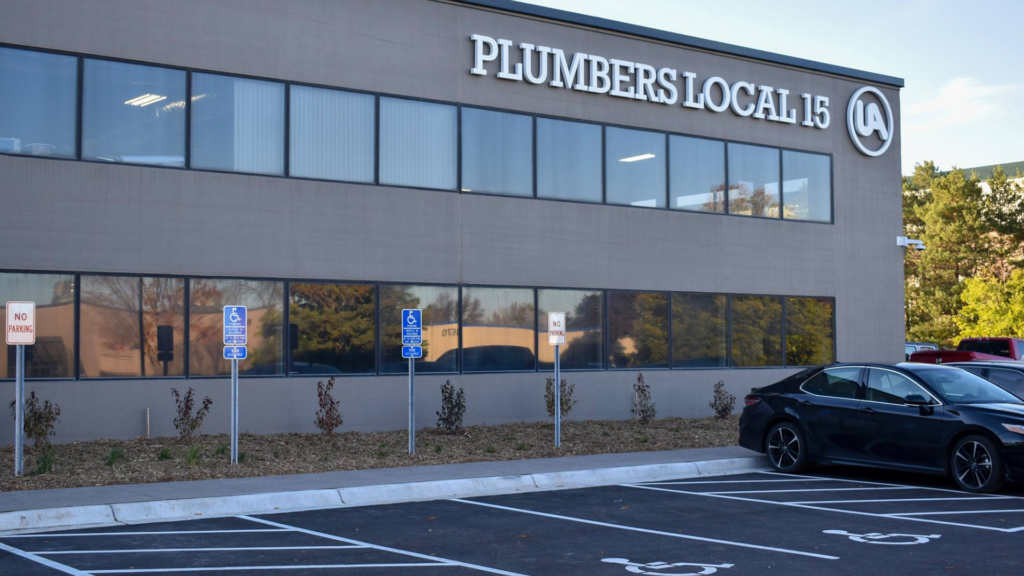